CORROSION
- Metals extracted from its primary ore (metal oxides) have a natural tendency to revert to that state under the action of oxygen and water.
- Corrosion is an electro-chemical process that involves the passage of electrical currents on a micro or macro scale by an “anodic” reaction.
- This reaction produces free electrons, which pass within the metal to another site on the metal surface (the cathode), where it is consumed by the “cathodic” reaction.
- Corrosion process is initially caused by:
- Difference in natural potential in galvanic (bimetallic) couples. Metallurgical variations in the state of the metal at different points on the surface.
- Oxygen rich areas become the cathode and oxygen depleted areas become the anode.
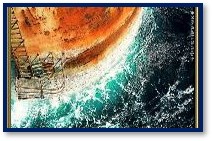
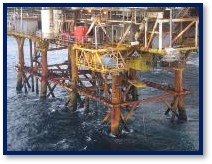
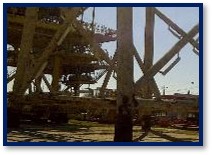
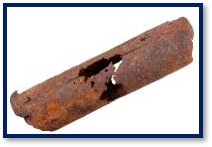
CATHODIC PROTECTION
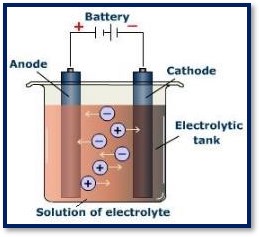
- The principle of Cathodic Protection is in connecting an external anode to the metal to be protected and the passing of an electrical dc current so that all areas of the metal surface become cathodic and therefore do not corrode.
- The current is a result of the potential difference between the two metals.
- Causes a positive current to flow in the electrolyte, from the anode to the steel.
- Surface of the steel becomes more negatively charged and becomes the cathode.
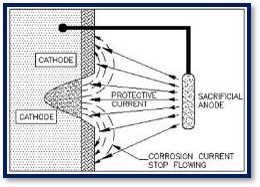
- A Galvanic System requires:
i) Sacrificial anodes
ii) Direct welding to the structure or a conductor connecting the anode to the structure
HOUSTON ANODES GUARANTEE
Homogeneous alloys always conforming to exact international quality standards and specifications.
NACE SP-0387 & SP-0492, DNV RP B401, ISO 155589-2, NORSOK M-503
Houston anodes are fabricated using only raw materials of the highest purity, assuring superior electrochemical and chemical properties.
Our team of professional engineers, manufacturing and sales personnel are committed to provide the best products with unparalleled customer service.

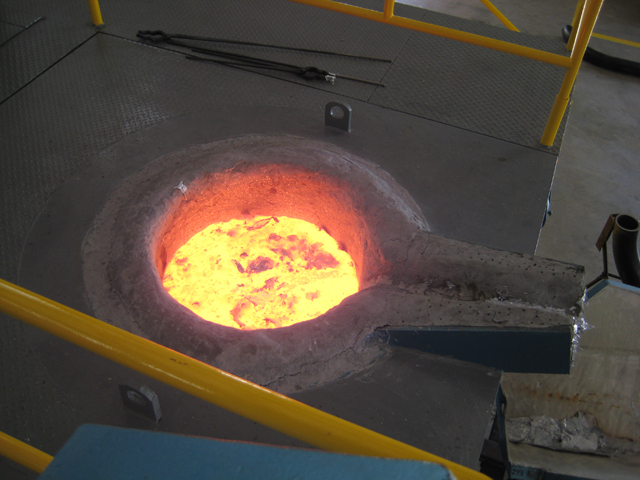
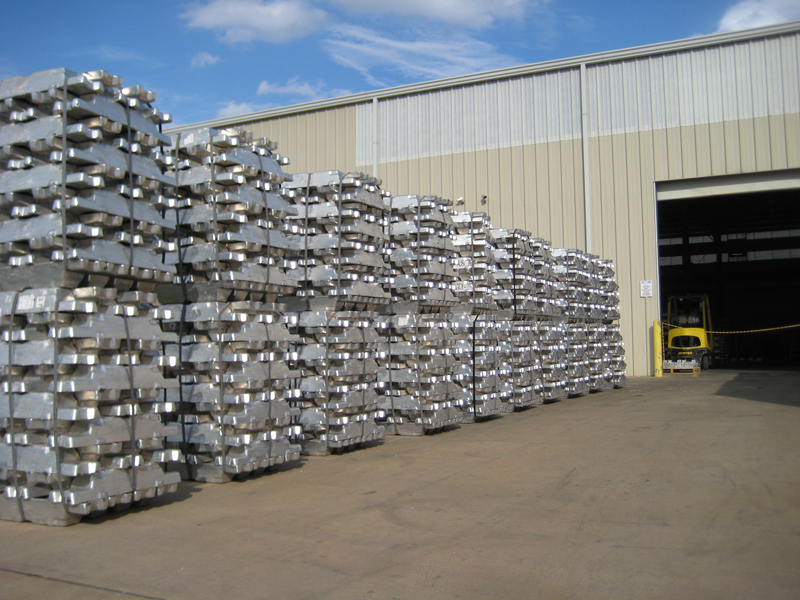
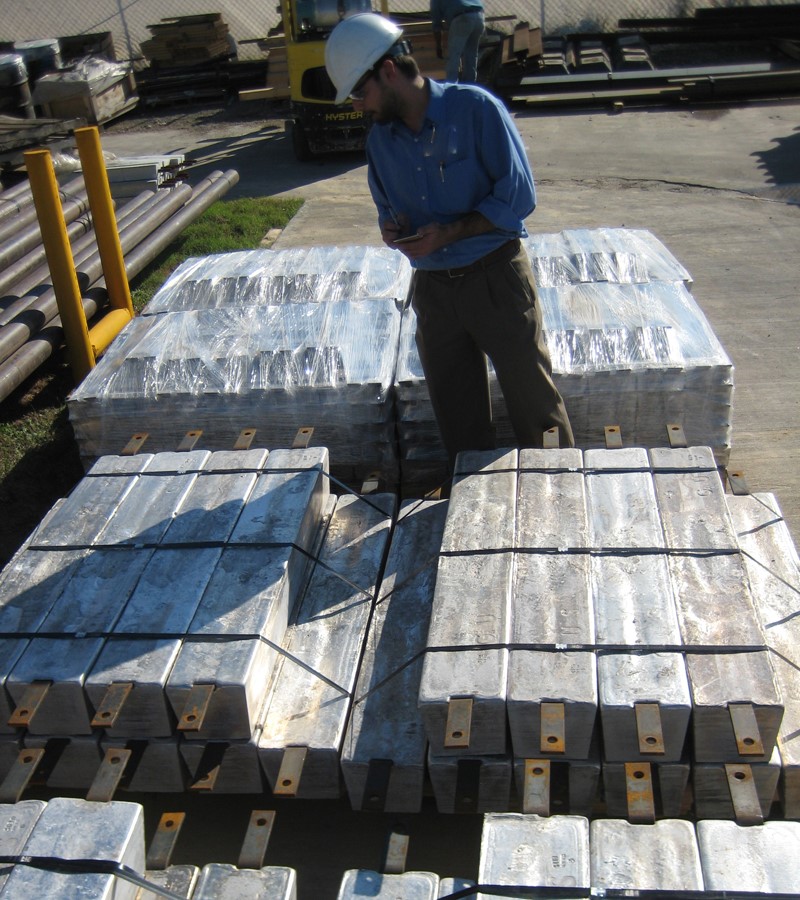
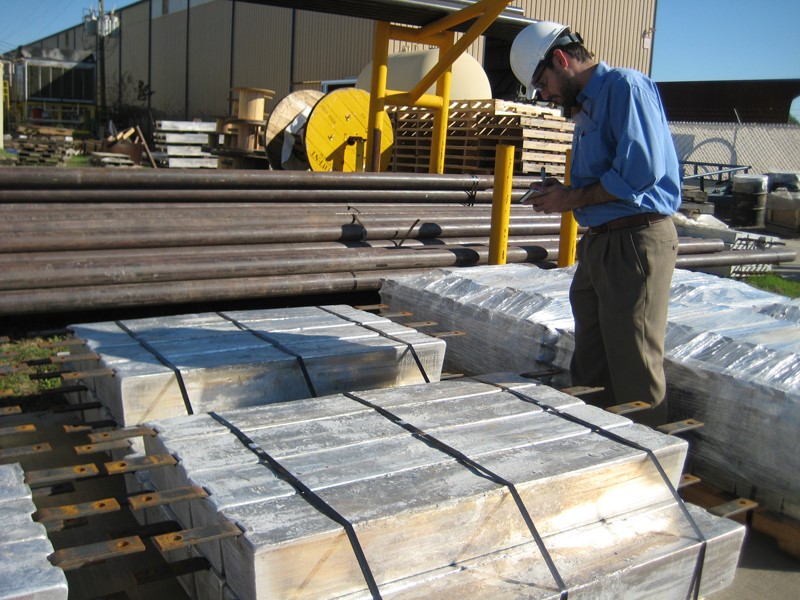
QUALITY CONTROL
- In-house state-of-the-art Laboratory equipped with a Bruker-Quantron Magellan Q8 spectrometer.
- All raw materials inspected and tested upon arrival prior to release for production.
- Chemical results verified against MTR’s.
- Chemical analysis performed on every heat.
- Electrochemical properties performed on every batch according to NACE TM-0190.
- Rigorous Inspection and Testing Points.
- Scheduled equipment calibration per OEM.
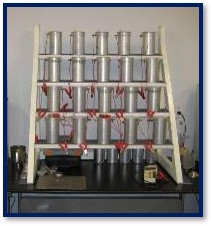
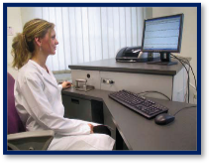
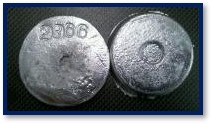
RAW MATERIALS
Primary High-Grade Raw Materials
Premium US and global suppliers
Primary Aluminum - 99.9% purity
Special High Grade Zinc - 99.99% purity
Indium - 100% purity
ASTM Steel - anode cores & mounting structures
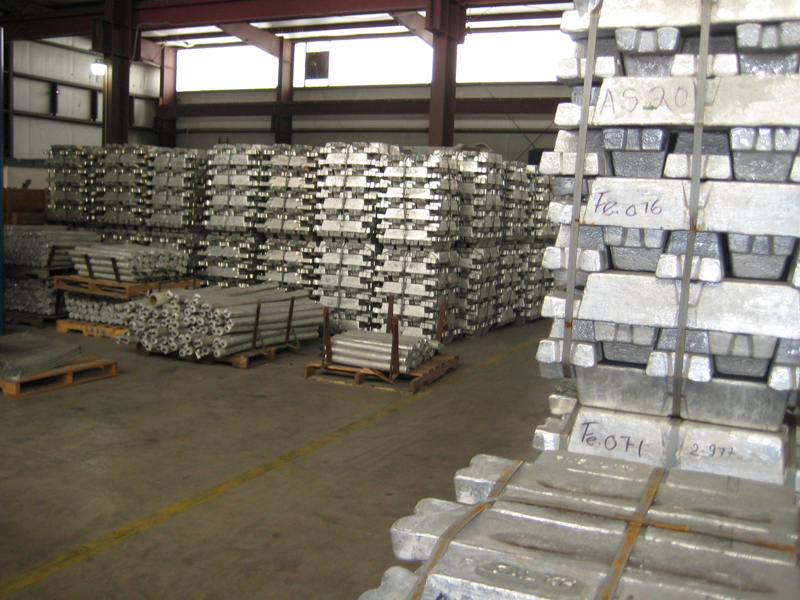
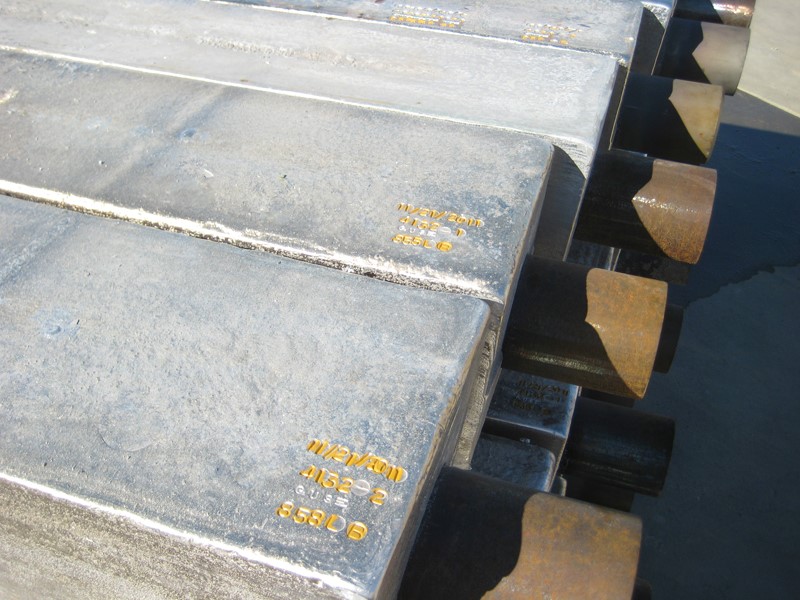
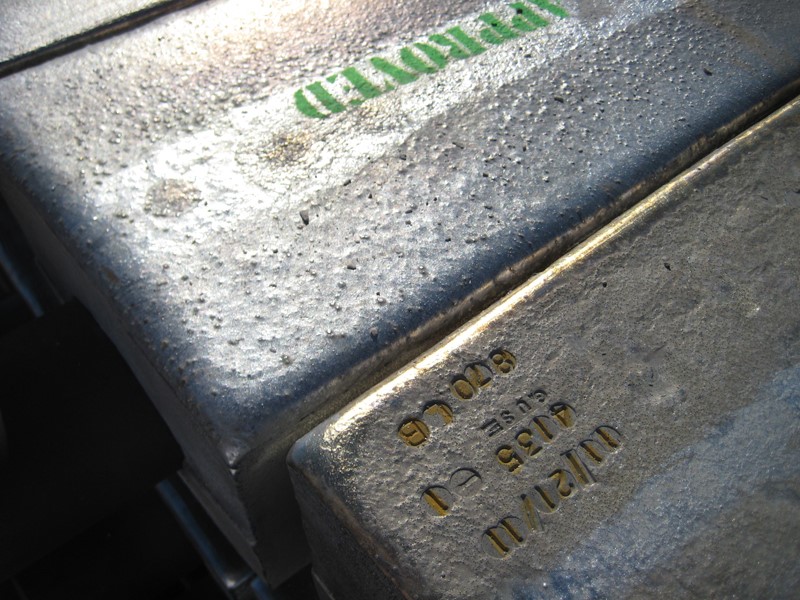
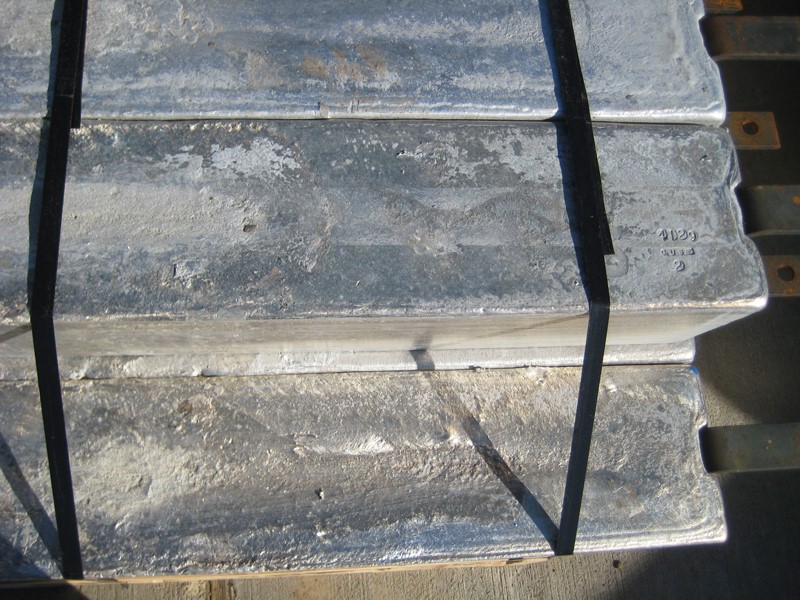
TECHNOLOGY
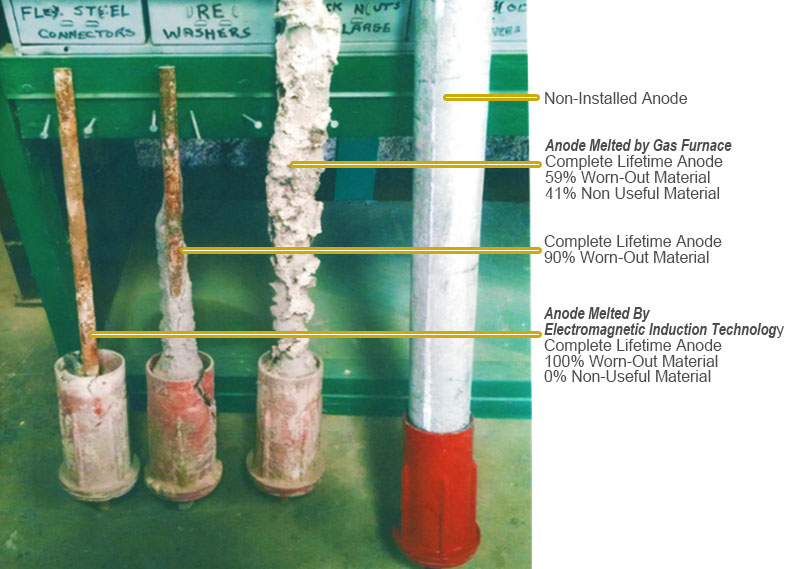